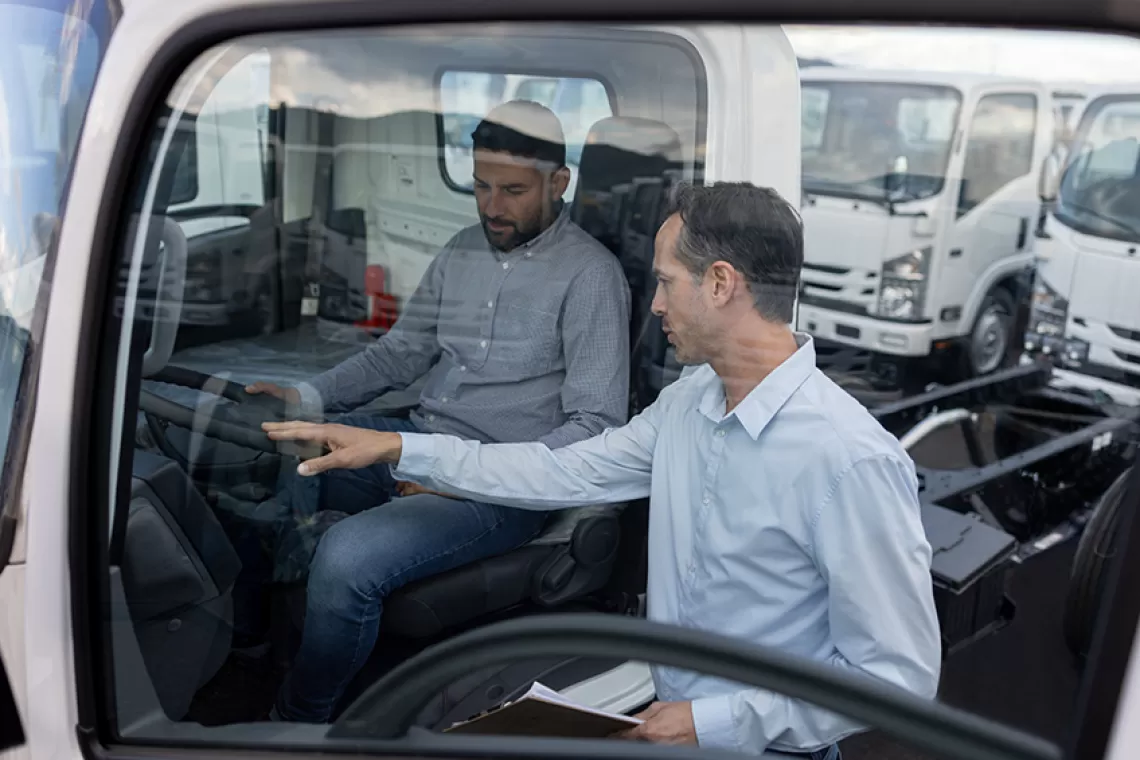
Building Accountability for Safety Leadership
Safety is about Leadership: Placing employee behavior at the frontline in establishing a culture of company safety
From real-life experience and on-site research, leadership safety support—from supervisors to CEO—must be actively visible to be optimally effective.
For many years, leadership as it relates to safety has often been defined as support, which at times translates to just don’t impede the process. Traditionally, leaders at the highest levels of an organization have fulfilled their mandate for such support by including safety in the corporate mission statement and the operational budget. Of course, behavior-based safety (BBS) professionals have known for quite a while that the success of our efforts hinges upon how adept we are in building leadership support for BBS systems. However, over the years, our interest in, focus on, and definition of leadership support has evolved . . . and for good reason.
From real-life experience and on-site research, leadership safety support—from supervisors to CEO—must be actively visible to be optimally effective. Leadership at each level has changed the role of leadership. Why? Because the evidence reveals that doing so is necessary. For example, the data from one early study, published in Professional Safety Magazine, shows that when leaders perform safety observations/walk arounds in their facilities and are actively engaged in those observations, a higher level of participation in safety observations from employees occurs, a key part of a successful BBS process. (McSween, 2000, see graphs below.) Employees become the leaders in achieving a safe environment for themselves and others.

In facilities where leaders do 80 percent of the observations they are scheduled to do, those facilities average better than 60 percent voluntary employee participation in conducting BBS observations. Our research also reveals that this type of active leadership involvement isn’t only important during the first year of implementation; it becomes even more important for sustaining such initiatives (see the second graph below). We have replicated this correlation in a variety of other organizations.
From my perspective, this correlation is not so much about leadership modeling the behavior, but rather it appears to affect a leader’s credibility. That leader can be at the top with his direct team or leaders throughout levels of the organization—managers, supervisors, and onsite observers connected to leading and directing the work. In other words, when the leaders asked their reports to participate by conducting safety observations and feedback, the credibility of that request is higher if the employees see that the leaders make time to conduct safety observations and provide feedback. There is a clear relationship between what is said and what is done to increase safe behavior in relationships between those who direct and those who do the work.

Leadership Is Important
Employee Participation as a Function of Leadership Observations
This discovery was a big deal in the early stages of behavior-based safety because in those early days many of our competitors were implementing behavioral-observation systems that only involved employees. (Some BBS consultants still take that approach.) However, with data supporting our approach, we began to routinely track leadership participation. Today, if a company wants a behavior-based safety process but they don’t want us to work with leadership, we always point out the gap between what is expected and what is done. Each level of leadership provides a great deal of visible commitment to the ideal of keeping each other safe. A basic report allows leaders to see who is doing observations and the number of total observations they’ve done over any period. The range can be from one month to twelve months. With this report, those individuals who take on the role of designated observers and/or supervisors, stand out and such supportive information can be incorporate into individual performance appraisals. Typically, this remains the bare minimum of our intervention in working with leadership when implementing a BBS process. More typically, however, we now bundle an intervention focused on leaders throughout the organization, and on getting them more engaged in promoting safety, parallel to the implementation of our behavioral-safety efforts with the addition of learning architectures (motivational and captured resource improvements) built into the day-to-day activities of the operation. In other words, our projects have a co-equal focus on BBS and safety leadership and structuring the workplace culture with the motivational systems to sustain learning and change as needed across the safety arena.
In his article “Exploratory Analyses of the Effects of Managerial Support and Feedback Consequences on Behavioral Safety Maintenance” published in the Journal of Organizational Behavior Management, Dominic Cooper makes the overall point that employees need to see leaders doing something to support safety every week. In the case of BBS, it is probably not as critical that the something is a safety observation, but employees need to see leaders at every level engaged in activities that promote safety; whether they ensure that a safety-related work order gets addressed, do a safety observation, provide feedback, host a safety meeting, or participate in a safety committee meeting. The takeaway from his work is that companies of any size need to focus on visible safety leadership.
When Atul Gawande’s excellent book, The Checklist Manifesto: How to Get Things Done Right was published, I was a bit disappointed that he didn’t mention behavior-based safety. In the BBS field, we have used checklists extensively for some time, including those around leadership behaviors (sometimes as simple as a yes/no pertaining to doing a certain behavior or a frequency count). Gawande’s book provides many ways to structure checklists. We have found it easier, when talking with leaders, to talk about structuring their agenda for safety and what they’re going to cover in their staff meetings, rather than talk about the leadership checklists we have used for the past fifteen years. Much can be learned from what leaders believe they need to do to move the essential mission ahead every day.
Senior managers find it more acceptable to talk about a creating a systematic review of a structured, recurring agenda at each level of the organization, rather than creating and reviewing data from leadership checklists at each level of the organization. The way we talk about it has changed; the format of what are essential elements of a checklist has changed, but the process creates the same, or better, level of accountability for leadership practices in support of safety.
Granted, at times a leadership checklist may be more appropriate, for example when there are a variety of behaviors. The checklist may provide a better prompt or provide better guidance. We achieve better success with structuring the agendas and sharing the outcomes we hope to achieve together, at different levels of the organization. Additionally, agendas have some advantages over checklists. With leadership checklist we are tracking leadership behavior the same way we are tracking the safety practices of employees: entering the data into computers, creating reports, and so forth.
When a company’s leadership uses a structured agenda, the leaders can develop a workable process for each of their direct reports, such as a notebook with dividers to track what they need, more conveniently tracking their safety activities. This approach also provides other advantages, flexibility being one of the main issues. Leaders may be talking about lockout/tag-out issues this month, but (possibly driven by the observation data or near-miss data or, worse case, incident data) they can easily change the focus for the following month. They can cascade this method in a systematic way down through the organization, increasing alignment and accountability for both safety and BBS. The list below summarizes the key considerations in each approach.
SAFETY LEADERSHIP CHECKLISTS
- Distinct checklist of critical safety leadership practices
- Strive for consistency
- Adds recording and reporting tasks
- Computerized reporting
- Formal reports
RECURRING AGENDA ITEMS
- Agenda defines a few critical behaviors
- Flexible, can change focus
- Builds on existing structure
- Recording done in meeting minutes
- Paper/binder based
Cascaded Coaching
One of QSE’s clients experienced an interesting problem: All of their incidents in one division occurred when a supervisor wasn’t present. This may sound odd, but this particular division was comprised largely of remote workers, usually out in the field and separated by many miles. During the assessment, we looked at the points of contacts between each level of leadership and the next, from the director down through the frontline employees. The director had a weekly staff meeting with his managers. During this meeting, the first agenda item was always safety. They routinely went beyond the reviewing incidents and discussed safety observations, near misses and safety action items. Managers routinely talked with leads via cell phone or in person to discuss daily schedules and assignments. These discussions also routinely included the above-mentioned topics, often adding encouragement to their leads to conduct safety observations. The leads always started each day with a tailgate safety meeting that would include a review of JSA’s, discussing the potential hazards, and how to mitigate those hazards. Leads often had multiple jobs, so once the tailgate was complete, they would designate an employee to take the lead on the job and then would take a portion of the crew and go to another jobsite. Finally, late in the day, the lead would place a cell-phone call to the designated employee to check progress on the job.
They were doing many things right, but we worked with them to fine-tune each point of contact to address practices that would help prevent injuries when the supervisors were not present. We positioned this as leadership development and asked each level to review the quality of the safety efforts at each level, with an objective of improving the quality of observations and discussions about safety on the job.
The Director began to ask managers about the discussion they had with their leads around safety and the quality of the tailgates. The managers began to talk with the leads about the quality of the conversations that took place at the tailgate meetings. Did they think that participants were involved in the discussions? How did other employees respond to the discussion? What did leads see them doing differently? How did what the designated employee say about their observations compared with what the lead observed when doing similar observations?
Part of the purpose of the conversations between the lead and the designated employee was to explicitly help the designated employee develop their safety leadership skills, and to more explicitly enlist and define their help in preventing injuries.
Finally, and this was perhaps most significant, we added a safety component to the final cell-phone call from the lead to the designated employee at the end of the day. We had the leads routinely start these phone calls with a discussion about the designated employees’ efforts to prevent injury. The leads asked if the steps discussed in the tailgate were successful in mitigating the hazards they had identified in their discussion. Further, they asked if conditions changed from what they had planned, and if so, what kind of hazards the change created, what kind of discussion they had with coworkers about the new hazards, what worked for them, and what they might do differently the next time they had a similar job.
As with the other levels, we provided a formal agenda to prompt these discussions, though the leads were encouraged to adapt the questions to the context of the job.
Close Calls (or Near-Miss Reporting)
Adding close calls (or more traditionally, near misses) to the BBS observation process is important. Any particular behavior that is identified unique to the culture in place can help to call attention to quick fixes and strengthen the ownership of such processes by those who best understand their conditions for error.
During the feedback discussions, observers ask their coworkers if they’ve seen any near misses. This seems to be a much better way of capturing near misses than requiring a scan of behavior that may be changed simply by observation but not really capturing all the near misses that might occur. Observers then write the details in the comments section of the observation form. The details get entered into the computer, and at the end of the month, a list is generated of all of the comments so that the safety committee has the opportunity to review them and conduct further analysis, taking action when necessary.
This process is fairly easy to do and provides a much higher rate of data on near misses, close calls, and minor first-aid kinds of injuries being noted than our clients ever got from other kinds of recording system even when compared to providing incentives for reporting these kinds of events. Reporting close calls in conversation is easier for the employees than filling out a formal report of the near incident.
The Safety Leadership (R)evolution
It is not enough to put safety first on the agenda, as if that signifies a company’s commitment. It is in what comes next that defeats in many ways the bold declaration in that statement about safety. The way most companies declare their safety-first commitment is by asking, “Did we have any injuries? Was there an incident or near miss?” and then if the answer is no, they go on to talk about other things, such as quality, production, and costs. If the answer is yes, they often issue pronouncements that those things must change and take disciplinary action against the employee. Often, injury reporting goes underground in those instances.
Behavioral safety is as much about safety leadership behaviors as it is about employee behaviors. The agenda for safety discussions in meetings at every level of leadership needs to include the questions, “What have you done to promote safety in the last week and what are you going to do in the coming week?” Most importantly, leaders at all levels need to also ask, “What can I do to support safety behaviors?” “What are issues that seem beyond your control that might cause unsafe actions?” In addition, they need to describe things they are doing and ask if those things are helpful. Those discussions should cascade through the organization with leaders at every level asking their direct reports what each of them can do to make a difference. These discussions should promote sharing new information throughout the organization. Finding good ways to share new learnings about their own behavior with their direct reports begins to shift the needle toward a strong belief in a culture of caring.
Preaching and talking about expectations is not as critical as first asking about the safe practices or concerns of employees, asking for how leaders, managers, and supervisors can help, and reviewing what is being done to promote safety, and only then providing direction or feedback—thus signaling the importance of everyone behaving safely. It is not the frontline employee or the leader that alone guides and directs safe accomplishments, but every employee doing what they can do for the good of all. These kinds of activities need to occur frequently. Therefore, we are very explicit about the purpose of BBS and leadership’s role in creating a culture where we take care of one another.
References: Cook, S., and McSween, T.E. (2000), The Role of Supervisors in Behavioral Safety Observations. Professional Safety, October, 33-36.