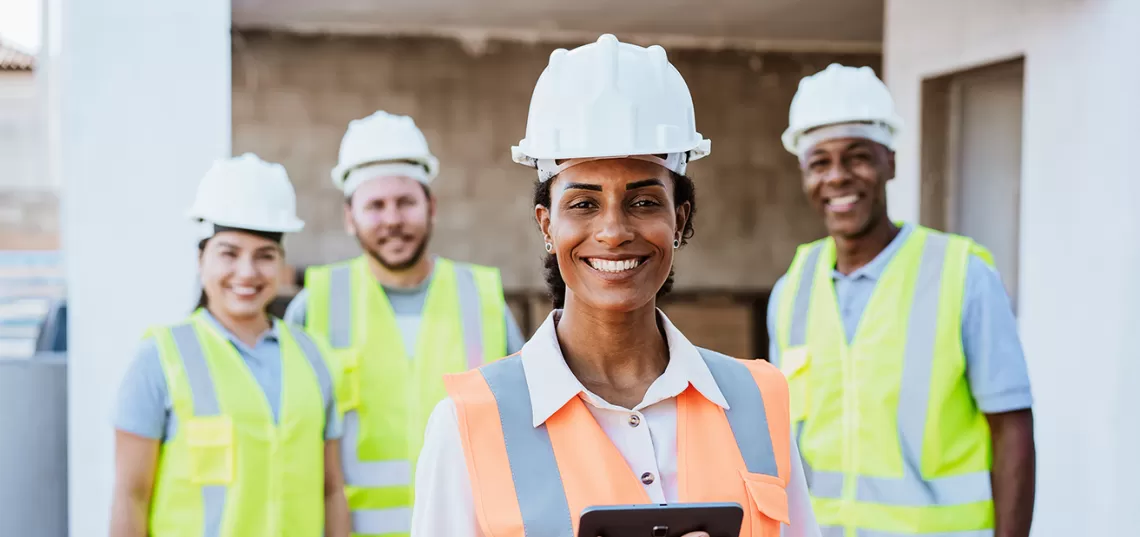
Keys to a Successful Behavior-Based Safety Process
An old adage in quality improvement efforts was, “Do it right the first time.” That statement is particularly relevant when it comes to behavior-based safety. As a good friend of mine likes to say, “You never get a second chance to make a first impression.” This statement is also relevant because behavior-based safety is much harder the second time around. Once you lose credibility in this kind of effort, getting it back is very difficult.
This is an intermediate to advanced paper that assumes that you have a basic understanding of behavior-based safety (BBS), a process that involves employees in conducting safety observations within their organizations. Conducting observations is typically voluntary. The names of employees who are observed are not recorded. Peer observations are not used as the basis for disciplinary action. Employees get immediate feedback as part of the observation. If these basic safety program elements are new to you, or if you don’t agree with them, you need to get a better understanding of what behavior-based safety is all about.
Having said that, I’d like to talk about typical problem areas that companies struggle with when implementing a BBS process, particularly when they try to initiate the process on their own or without the assistance of knowledgeable, outside assistance. These problem areas that I will address here include the following:
- Lack of logistics planning and preparation
- Generic or irrelevant checklists
- Inadequate training
- No systematic use of observation data for improvement planning
- Little or no reinforcement to support the process
- Poor leadership participation and support
I have observed these problems frequently enough to develop a well-defined set of keys to a successful process, each key addressing one of these common challenges.
The #1 Key to Success
Planning First, Training Second!
Many organizations have the mistaken belief that all BBS requires is to develop a checklist and train a group of employees how to conduct observations. This approach can create some benefits when the newly trained employees get excited about safety and begin conducting area safety observations. Unfortunately, such efforts are short-lived. In order to sustain observations, organizations first need to create a formal system or process to support observations. The system or process should include ensuring that the observation data gets summarized into useful information, that someone uses that information to promote safety improvement, that the information gets fed back to employees, and that the applicable safety committee or steering committee is actively managing the process. To this end, most organizations would be better served to invest the time to plan all of these logistical details about how the process should work prior to beginning observer training. Once the planning is completed, the organization can then train employees on the process to be used, not just the generic skills required for observations.
After more than 50 years of research, behavior-based safety systems improve quality and safety.
We further recommend that this planning be done by the employees who will be participating in the process, generally the steering committee or safety committee members. Such committees are typically made up of 8 to 15 participants, usually hourly employees along with a representative from safety, a representative from the organization’s leadership, and a representative from engineering. Getting this level of involvement from committee members ensures that they have an inside-out understanding of the process they created. They take pride in having created a safety improvement process and feel a high level of ownership for it. The only way we know to develop this kind of ownership is through meaningful involvement in planning the process.
The #2 Key to Success
Create Checklists Specific to Your Facility
To maximize the effectiveness of behavior-based safety, observation checklists should be specific to the kinds of risks experienced by employees working within the organization. All of the research studies used checklist specific to the tasks being performed by the employees. Generic checklists can be effective in increasing attention to safety, but the ideal is to increase the focus on behaviors that have contributed to past injuries, and not only within your facility but within each area in your facility. Checklists need to be created based on your experience, not the experience of other organizations with different processes, practices, and cultures. We encourage our clients to create checklists that list work practices in order of their contribution to injuries—that is, the practices that would have historically prevented the most injuries should be at the top of the checklists. This way the checklists become an integral part of your safety training and orientation. New employees who participate in observations are learning the behaviors that are most important in reducing their risk of injury.
After more than 50 years of research, behavior-based safety systems improve quality and safety.
Generally, organizations should try to identify “practices” rather than specific behaviors. Practices must be defined clearly enough that they can be reliably identified, but not have a level of detail that would result in a checklist for every procedure. “Working clear of the line of fire” is an example of a practice that would help employees avoid injury in many organizations. Behaviors that exemplify this practice would include not working in front of a pressure-relief valve, not working under a platform with employees who might drop a tool, not working behind mobile equipment that could become engaged, or in an office environment, not standing in front of a door that someone might come bursting through. In comparison, defining every possible behavior that might make up “the line of fire” would be cumbersome.
The #3 Key to Success
Provide Observer Training for All Employees
All employees have specific training needs when implementing behavior-based safety. Employees conducting safety observations need to be able to recognize hazards and provide feedback based on their observations. Other employees need an introduction and kick-off event that helps them understand the new process. The goal is to ensure that they are supportive and less resistant to the process because they know what to expect. The observer training should build on that understanding and include both the rationale for the process and the construction of the applicable checklists, as well as actual practice in conducting observations and providing feedback on observations. Employees can practice observations using video scenarios and role-playing and, in some cases, pairing up with another observer (or Steering Committee member) and going into their work area, conducting observations with feedback, then coming back into the classroom to debrief regarding the experience. Such training typically requires four to eight hours for each employee. As a rule, organizations should train 10-15 percent of their employees to conduct and discuss safety observations, with the goal of rotating all interested employees through the position over the years following implementation.
Two other types of training should be part of the implementation plan. First, the Steering Committee members must understand how to conduct their monthly meetings, with each member fully trained to fulfill their role in the meeting. Typically, each member has a specific role such as analyzing observation data, managing the action plan, communicating with leadership, sharing BBS information in safety meetings, and other roles critical to maintaining a successful BBS process. Finally, leaders should be trained in their expected roles for supporting the BBS process. The ideal training for leaders includes a discussion of their personal value for safety and defining behaviors that demonstrate their value for safety in the workplace.
The #4 Key to Success
Use Observation Data to Improve Safety
Organizations often struggle with sustaining participation in observations. Employees submit their completed observations, but then the data just seem to go off into a hole somewhere. They never see anyone doing something with the observation data. In these cases, employees invariably stop participating, after which the process grows stale and eventually dies.
Ensuring a lasting process requires that organizations establish a formal process for using the observation data to plan safety improvements. Typically, the safety or steering committee reviews the observation data during monthly meetings. Ideally, they will create a Pareto diagram to help identify the safety practices that will have the most significant impact. The committee may select improvement targets based on frequency, consistency, or potential severity. After identifying the top improvement targets, the committee should further analyze the data to identify when and where the at-risk behaviors are most apt to occur. Based on this analysis, the committee should develop an action plan that addresses both behavioral and facility issues that contribute to the at-risk behaviors. If called for, the action plan should change the physical facilities and the management systems (including training, procedures, and leadership practices) as well as the focus within the behavioral safety process in ways that encourage and support the safe practices targeted for improvement. When the safety committee implements the action plan, particularly with regard to physical changes, it needs to ensure that the changes are communicated throughout the organization so that employees know the changes are being made on the basis of the observation data.
The safety committee is also typically responsible for communicating data from observations. They may do this by posting observation data on safety bulletin boards in work areas or by reviewing the data in safety meetings. Ideally, they will use graphs to visually communicate the observation data, often including the Pareto diagrams that show why they targeted specific behaviors for improvement and trend charts that will show the improvements achieved in target behaviors.
The #5 Key to Success
Use Recognition and Celebrations to Support Safety Efforts
The topic of safety awards has been hotly debated over the past couple of years. I believe they are important but that companies need to use them wisely. The big concern about safety awards is that they can have a chilling effect on employee willingness to report incidents and injuries. If employees do not report minor injuries, we may miss the opportunity to learn from incidents that could have been more significant. In addition, safety awards programs by themselves often provide very little motivation for working safely on the job. The typical award program is based on working some period of time without injury. Imagine two employees who work together basically doing the same job. One of the employees works safely day in and day out, following every safety procedure without compromise. The other employee is also a good employee, perhaps even a little more productive because he is willing now and then to shortcut a safety procedure now and then. Chances are that neither of these employees experience an injury and at the end of the year, we treat them both exactly the same in providing each one the same safety award even though they are different in the extent to which they work safely on the job. Finally, in interviews with employees, they routinely tell us such awards do not motivate them to work safely.
Still, we believe that recognizing safety milestones is important as it is one of the vehicles through which an organization communicates its what it values. So, celebrating a million man-hours without a lost work-day case is important. On the other hand, leadership should not “dangle the carrot” a few months be-forehand by making comments such as, “If you go three more months without a lost workday injury, we’ll serve a steak dinner for all employees.” The celebration should simply come after the achievement, without enticing employees in a way that might influence their reporting.
Still, we believe that recognizing safety milestones is important as it is one of the vehicles through which an organization communicates its what it values.
Recognition and celebrations are also important elements in supporting behavior-based safety efforts, particularly in maintaining long-term participation. The employee safety committee should monitor data from the process and provide recognition for individual contributions to safety and arrange celebrations of team successes. They should generally use recognition to support individuals conducting observations and quality observations, reporting near misses, and participating individually in other ways. Likewise, they should arrange for teams to celebrate improved participation, safety improvements, and achieving other team safety goals or targets. The safety committee must needs to realize that recognition and celebrations are on-going programs and as such will need to be continually changed and tailored to the individuals being recognized. Generally, involving employees in these activities results in a much more effective recognition process than when these programs are planned only by management and supervisory personnel. The idea is to ensure that, in order to create safety champions, you have an on-going process to recognize employees who champion safety in order to create safety champions.
The #6 Key to Success
Train Leaders in Their Roles
Our belief is that everyone should be involved in the behavioral safety process. Otherwise, behavior-based safety efforts too often contribute to divisions between management and employees. We want to create a process that pulls people together, not one that drives a wedge between persons at different levels of the organization. With this in mind, when designing a behavior-based safety process, the design team should carefully plan the roles and responsibilities of all employees, particularly managers and supervisors. Leaders clearly understand their roles as well as know how to support the process as the design team intended.
Furthermore, research shows the benefit of involving supervisors in conducting observations. When managers and supervisors participate in conducting safety observations, a greater percentage of employees also participate in safety observations. Personally conducting observations places leaders in the role of walking the talk when they encourage employees to participate in safety observations. Otherwise, the message is very clear, “Do as I say, not as I do.”
Some Final Suggestions
One of the key concepts of this paper is that behavior-based safety is about creating a system, not simply training a group of observers. It is not about changing people or carrots and sticks or Band-Aids, but rather creating a formal process that encourages everyone to get involved in safety improvement. Here are some additional suggestions:
Suggestion 1:
Don’t use a cookbook approach. This article provides a set of guidelines, but your success depends on your ability to plan the application of these ideas in the context of your organization’s culture. This suggestion pertains to the approach described in this article as well as to comparable approaches from various consulting organizations around the country. Don’t simply buy a package. Make sure you use the approach’s key elements to develop a system that meets the needs of your organization. On the other hand, don’t be too quick to discard key elements just because they are difficult to implement or maintain in your organization.
Suggestion 2:
Plan and clearly define management’s role. The observation process requires time and a great deal of effort. It will require active support from all levels of management. Pay special attention to the suggestions for involving management and defining management’s role in the process. Management’s role will be the critical factor in both the long-term success of your observation process as well as the day-to-day elements of your safety improvement process.
Suggestion 3:
Maximize participation in the final design. The only way to create ownership is through meaningful involvement in the design process. This process requires a high level of involvement and has several options for ways to involve people. Don’t make the mistake of designing a safety process in a vacuum and then trying to implement the program by mandate. Involve people in the design at each stage. Then have those who assist with the design take it back to their work areas and get input and suggestions from their colleagues.
Suggestion 4:
Create a different checklist for each area. The research studies all used checklists of specific safe behaviors that were job- and area-specific. Unless you are in a small facility, do not try to develop a generic checklist that works for all areas. Maintenance has different safety requirements than a laboratory, for example, and their checklists need to look and be different. To maximize the value of the checklists, they should be explicit enough to address the specific, safe practices of different job functions.
Suggestion 5:
Don’t create a bureaucracy around the data. The value of this process is in getting everyone to pay attention to on-the-job safety, not in creating a paper storm. Build informal systems of accountability based on the observable parts of the system. Don’t create an elaborate system of paper reports. Do pay attention to the safety process during informal contact with individuals in the work areas and during formal meetings at each level of the organization.
Suggestion 6:
Use classroom training only when needed. Place emphasis on designing a training process that satisfies your needs, not putting all employees through observer training. Provide enough training to create the understanding that people need to support the process. Also, don’t think of training as strictly a classroom process. When training observers, for example, an on-the-job mentoring process is often more effective. Use training only when it is appropriate and select an appropriate process for delivering the training that’s needed.
Suggestion 7:
Persevere. Don’t quit – ever! False starts characterize the implementation of any significant new process. Implementation is often two steps forward and one step back. The key to success is continuous improvement. Learn from each of your steps so that you can do it better the next time. Just keep fine-tuning your process until you achieve zero accidents. Then strive to maintain that level of safety excellence.
About the Author
About ABA Technologies
ABA Technologies specializes in the application of the science of behavior. We partner with organizations to help them build a culture of learning and development that supports employees and organizational objectives. All business leads back to behavior—are employees doing the right things, in the right ways, at the right time? Our behavior-based systems approach looks at employee performance within the organization’s ecosystem and pinpoints variables that affect people and business outcomes. Our learning architectures help fill skill gaps, create happy and productive employees, reduce turnover, impact leader behavior, and promote safe and secure workplaces.
While evolving technologies and shifting work. force make business unsteady to navigate, ABA Technologies is your partner to continuously improve behavior and business.